Collaborative robots, or “cobots”, are a new type of robot designed to work safely and effectively alongside humans in factories, warehouses, and other industrial settings. While traditional industrial robots are large, expensive, and require a dedicated operator, cobots are smaller, less expensive, and easy to use.
Cobots have been designed with human safety in mind, with sensors and software that allow them to stop and avoid collisions. This makes them ideal for working alongside humans in close proximity. Cobots can also be easily programmed to perform a wide variety of tasks, making them versatile and adaptable to different work environments. As the cost of cobots continues to fall and their capabilities continue to increase, it is likely that we will see more and more of them being used in industries around the world.
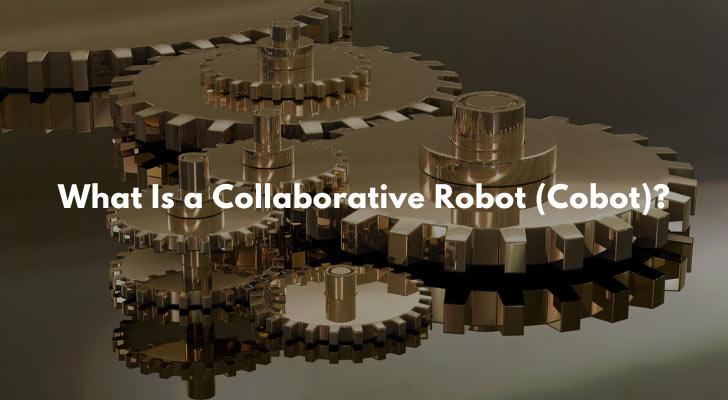
What Is a Collaborative Robot?
A collaborative robot, or cobot, is a robot that works alongside humans in a factory, office or other workplaces. Cobots are designed to assist humans in performing tasks that are difficult, dangerous or repetitive. They are typically used in manufacturing and assembly operations.
Cobots are becoming increasingly popular as they can improve worker safety and productivity. For example, a human worker might be lifting heavy objects or working with dangerous chemicals. A cobot can be used to lift objects or handle chemicals, reducing the risk of injury to the human worker.
Cobots can also be used to perform repetitive tasks such as welding or painting. This can free up human workers to perform more complex tasks. In some cases, cobots can even be used to train human workers on how to perform a task.
The Benefits of Using Cobots
There are many benefits of using collaborative robots in manufacturing and industrial settings. Cobots can help increase productivity while reducing costs. They can also help improve quality control by providing consistent and repeatable results. In addition, cobots can help reduce on-the-job injuries by working alongside humans and taking on tasks that would otherwise be hazardous.
One of the biggest benefits of collaborative robots is that they can help manufacturers stay competitive in the global market. By automating tasks that are typically performed by human workers, manufacturers can reduce their labor costs and increase their output. This allows them to compete with other manufacturers who may have lower labor costs but less productive workers.
In addition to helping manufacturers stay competitive, collaborative robots can also help create new jobs. As cobots increasingly take on more tasks in manufacturing and industrial settings, human workers will be needed to oversee and maintain the robots. This creates new opportunities for employment in these industries.
To summarize, the benefits of using collaborative robots are;
- Worker safety: Collaborative robots can be used to do jobs that are difficult or dangerous for humans, such as lifting heavy objects or handling hazardous materials. This reduces the risk of injury to workers.
- Productivity: Cobots can be used to automate repetitive tasks such as welding or painting. This frees up human workers to do more complex tasks. In some cases, cobots can even be used to train human workers on how to perform a task.
- Quality: By automating tasks and providing consistent results, cobots can help improve the quality of products.
- Flexibility: Cobots are designed to work alongside humans. This makes them more flexible than traditional industrial robots, which are often isolated from humans in cages.
- Cost: Cobots are generally less expensive than traditional industrial robots.
The Different Types Of Collaborative Robots
There are four main types of collaborative robots:
1. Cartesian Robots
These robots have three linear axes of motion that are perpendicular to each other, just like the X, Y, and Z axes on a Cartesian coordinate system. They are also known as “gantry” or “XYZ” robots. Cartesian robots are well-suited for tasks that require precise pick-and-place motions, such as assembly or packaging.
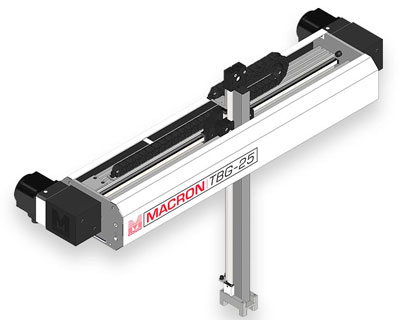
Belt driven 2 axis system designed for pick & place applications. Author: Midigital, Creative Commons Attribution-Share Alike 4.0 International license.
2. Cylindrical Robots
These robots have two rotational axes that are perpendicular to each other, like the X and Y axes on a cylindrical coordinate system. They are sometimes called “polar” robots. Cylindrical robots are often used for welding and material handling tasks that require more than one axis of rotation.
3. Spherical Robots
These robots have three rotational axes that intersect at a single point, like the X, Y, and Z axes on a spherical coordinate system. They are also known as “coordinate measuring machines” (CMMs) or “three-axis positioning systems” (3APS). Spherical robots can be used for precision measurement tasks in manufacturing quality control applications.
4. Articulated Robots
These robots have at least three rotational joints that allow them to move in a wide range of directions. Articulated robots are often used for welding, material handling, and machine tending tasks that require a high degree of flexibility.
How Collaborative Robots Are Used
Collaborative robots, also known as cobots, are designed to work alongside humans in manufacturing and other industrial settings. Unlike traditional industrial robots, cobots are typically much smaller and lighter, and they often have built-in safety features that allow them to operate safely in close proximity to people.
There are a variety of ways that collaborative robots can be used in manufacturing and other industrial applications. One common use case is as an assistive device for human workers. For example, a cobot might be used to help lift and move heavy objects, or to perform repetitive tasks such as welding or painting.
Another common use case for collaborative robots is an automated work cell controller. In this role, the cobot is responsible for managing the flow of materials and products through a manufacturing process. This may involve tasks such as loading and unloading parts from machines, or assembling products from individual components.
Cobots can also be used for quality control purposes. In this application, the robot is equipped with sensors that allow it to inspect products for defects. This can help to improve the quality of finished goods while reducing the need for manual inspection by human workers.
Finally, collaborative robots can also be used for educational or research purposes. For example, universities and companies often use cobots to teach students about robotics and automation technology. Similarly, research laboratories may use cobots to conduct experiments or test new robotic technologies.
The Future Of Collaborative Robots
There is no doubt that collaborative robots, also known as cobots, are revolutionising manufacturing and other industries. With their ability to work safely alongside humans, cobots are opening up new possibilities for how work can be done.
Looking to the future, it is clear that cobots will only become more prevalent and important. As companies seek to increase efficiency and productivity, while also reducing costs, the use of cobots will continue to grow. Additionally, as technology advances, cobots will become even more capable and sophisticated, able to handle an even wider range of tasks.
While there are many exciting potential applications for collaborative robots in the future, some of the most promising include:
Automating repetitive or dangerous tasks:
Cobots can be used to automate tasks that are repetitive or dangerous for humans to do. This can help improve safety in the workplace and also increase efficiency.
Working in difficult or challenging environments:
Due to their rugged design and construction, collaborative robots can be used in environments that would be too difficult or challenging for humans to work in. This could include hazardous environments or tight spaces.
Assisting human workers:
Cobots can be used to assist human workers with tasks such as lifting heavy objects or providing guidance and assistance during complicated processes. This can help improve worker productivity and safety.
For $299/year or $149/quarter
Thrive Suite Includes: